Example below shows GRIPflow® material savings/part = 0.10 lbs. Material savings for 1 million parts = 100,000 lbs.
Fineblanking 4 Cavity Strip Layout
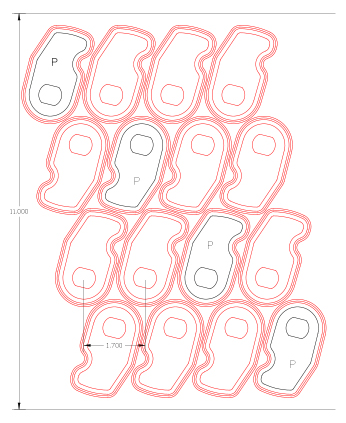
- The impingement ring uses more material
- Material thickness= .250”
- Pitch between parts= 1.700”
- Strip width = 11.000”
- Material/part required = 0.39 lbs
GRIPflow® 4 Cavity Strip Layout
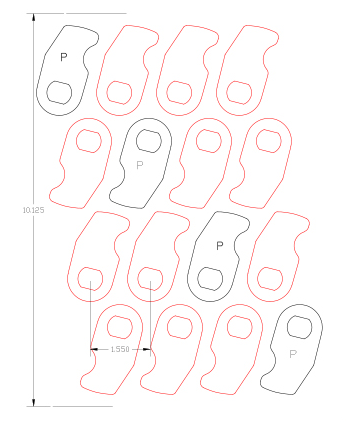
- No impingement ring
- Material thickness= .250”
- Pitch between parts= 1.550”
- Strip width =10.125”
- Material/part required = 0.29 lbs
GRIPflow® vs. Fineblanking
Like that of traditional stamping, the GRIPflow® slugs drop through the bottom of the die and bolster. Fineblank tooling is not able to have an opening on its bottom (this would be the press ram) due to the press piston and hydraulics beneath the ram – they must eject all slugs out with the stamped parts and, if any of these slugs stay within the tool, there is the possibility of tool damage.
The design and manufacturing methods for GRIPflow® tooling are streamlined and efficient as compared to its competitor’s cumbersome and antiquated design. GRIPflow® tooling typically costs 20% to 50% less than fineblank tooling.
The same is true with GRIPflow® presses – their design is not as complex as that of fineblanking and so their cost is less than fineblank presses. The fineblank process using the V-Ring also requires separate and additional tonnage – as much as 40% of the blanking tonnage – resulting in the need for more tonnage and larger presses than GRIPflow®
Conclusion
Customers are saying GRIPflow® stampings are much better than fineblanked stampings. Let GRIPflow® be your cost-saving solution for the 21st century.